IN THE COURSE OF PUTTING this book together, while disguising myself as a writer I chanced to interview a former law enforcement
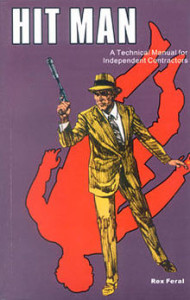
officer with twenty seven years experience for his opinion of how a perfect hit would go down. It was the opinion of this officer of the peace that the perfect hit would start with the purchase of a nondescript automobile, then driving, with tools in tow, to the jobsite.
Once there, he would follow the mark until a routine was established and probably waste the man in a public place with a blast from a double barreled sawed-off shotgun. Then he would throw the gun down and drive away while the bystanders were in a state of mass hysteria.
Even if he got caught with the shotgun in his hands, he argued, they would not be able to prove that the blast from that shotgun was the murder weapon since shotguns are untraceable. Obviously he has not kept in touch with new investigative procedures and techniques, for it is now known that each shotgun makes an individual and distinct spread pattern and the gun most certainly can be matched as the murder weapon.
“Why not hit the mark in his own home?” I inquired innocently.
“Oh, I’d never hit a guy in his own house,” he answered, “Too many witnesses .. you know, family … nosy neighbors and the like.”
What about a small caliber handgun with an attached silencer?” I asked.
“Well,” he answered, “You would have to carry the handgun concealed, and that’s against the law. But the shotgun, if it were a legal sized shotgun, you could carry that right in the window of your pickup truck on your gun rack. And I’d never touch a silencer. Boy! They’d burn you if you got caught with a thing like that!”
I concluded the interview pretending to be in awe of his wisdom, while inside I was amazed by the ignorance behind his reasoning.
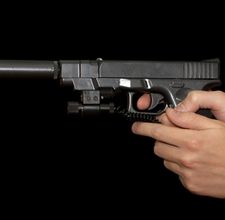
Why on earth, I thought, would a man worry about breaking gun restrictions when he was en route to commit a murder?
Yet, I felt comforted by his viewpoint. For his opinion probably represents the way a goodly portion of law enforcement officers think.
There have been many times when an amateur has just walked up to his mark on the street, blown him away in the midst of a crowd, ditched the gun in a garbage can and gotten away with it. But the whole procedure lacks professionalism and the risks are much too high.
The professional is on call to kill. He not only provides the employer with his gun, but with his expert knowledge, discretion and ability to carry the assignment off without needlessly endangering anyone but the mark.
The silencer is one of the most important tools a professional will ever have. The silenced weapon, when fired, will not draw attention. Lack of attention means more time. Time means getting the job done right. The panic, the pressure, is absent. There are many books available on the subject of making your own silencers. Most of the methods used require machine shop tools and the ability to use them with precision accuracy. This fact alone has put a lot of would-be professionals out of the game, or at least back into the ranks of amateurs.
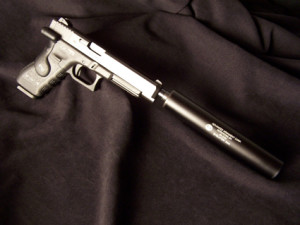
On the following pages, you will learn how to make, without the need of special engineering ability or expensive machine shop tools, a silencer of the highest quality and effectiveness. The finished product attached to your 22 will be no louder than the noise made by a pellet gun. Because it is so inexpensive (mine cost less than 20 dollars to make), you can easily dispose of it after job use without any great loss. Future silencers will cost even less to make, since many of the materials will not be used up in the first application.
Your first silencer will require possibly two days total to assemble (including drying time) as you carefully follow the directions step by step. After you make a couple, it will become so easy, so routine, that you can whip one up in just a few hours.
When it’s done, no need to take it out in the woods to try it out. Just stack some magazines or newspapers in a box and shoot to your hearts content in the garage. Believe me, it’s that good.
Just remember, as I mentioned before, to resight your gun after the silencer is in place. And when you do go out in the woods, experiment to test how your range is affected. You will lose some distance, and this must be taken into consideration later, when planning a hit.
DISPOSABLE SILENCER DIRECTIONS
The directions and photographs that follow show in explicit detail how to construct a silencer for a Ruger 10/22 rifle. The same directions can be followed successfully to construct a silencer for any weapon, with only the size of the drill rod used for alignment changed to fit inside the dimension of the barrel.
The following items should be assembled before you begin:
- Drill rod, 7/32 inch (order from a machine shop if not obtained locally)
- One foot of 1/4 inch brake line from auto parts
- One quart of fiberglass resin with hardener
- One foot of 1-1/2 inch (inside diameter) PVC piping and two end caps
- One yard thin fiberglass mat
- One roll of masking tape
- One 1/8 inch drill bit
- One 3/16 inch drill bit
- Handful of rubber bands
- Three or four single inch razor blades
- One sheet 80 grit sandpaper
- Six small wood screws
- One box steel wool
Cut a 10-inch section from the brake line. See figure 1. Drill a set of 1/8 inch holes down the length of the tube going in one side and out the other. The holes go all the way through. Notice in the photograph that the holes begin 1-1/2 inches from the end of the tube that fill on the gun.
Next, take a 3/16 inch drill bit and enlarge the holes. See figure 2.
Using masking tape and keeping the tape as free of wrinkles as possible, mask off about six inches of the gun barrel and the end of the barrel. Use only masking tape. Duct tape is too thick and would make for an improper fit. See figure 3.
Then place the drill rod down the barrel to keep the brake tube aligned. This perfect alignment is extremely important.
If the drill rod you purchase is a little too large, as sometimes happens, put it in a drill and using a file and sandpaper (80 grit), turn down the first six inches until it will fit inside the gun barrel. I operate the drill from the floor with my foot, letting the rod spin between my knees as I reduce the size. Check regularly until you achieve a perfect fit. If you grind the rod too small, cut it off and start over. Fit must be tight with no play. See figure 4.
Wrap glass mat around the gun and tube three times. Secure it with string or rubber bands every half inch to keep it tight and in place. The glass should be wrapped about two inches behind the sight and up to the first hold on the tube. See figure 5.
Now mix the resin. About a shot glassful will do. Mix it two or three times hotter than the package directions.
Brace the gun in an upright position and dab the resin into the glass cloth with a stubby brush. Keep dabbling until the cloth is no longer white but has become transparent from absorption of the resin. See figure 6.
As soon as the glass is tacky to touch without sticking (times differs according to weather conditions and humidity), it is time to remove the piece from the barrel. Move fast!
First, take a razor blade and cut a notch behind the sight so the piece can be removed. Then push on the glass to slide it off. Do not pull on the tube. See figure 7.
After removing the gun barrel, peel out the tape and allow it to finish hardening. You must work quickly. If you let the glass harden too much on the gun, you will have to cut it off and begin again.
Use a grinder and 80 grit sandpaper to smooth the hardening rough surface.
Next, grind the sides down about halfway, but do not grind past the point where the front of the sight makes contact. See figure 8. Cut it down until the barrel fits easily and snugly.
Stand the glassed inner tube upright in a vise.
Mix a small amount of resin and use an eyedropper to fill in any interior holes or air bubbles until the solid fiberglass is level with the steel tube end. This will give the junction of the steel inner tube and glass coupling added strength. See figure 9.
Clean the eyedropper with acetone.
Cut the PVC tube to desired length. This one is eight inches. See figure 10.
Drill a large hole in the center of one cap, making it large enough to fit on the glass end to the point where the sight makes contact.
Then drill small holes all around the cap at the bottom, as shown, with a 3/16 bit. See figure 11.
Wrap masking tape around the cap to cover the holes. See figure 12.
Stand the cap with the inside tube inserted into a vise. Get the cap level and straight with the tube.
Cut a lot of 1/2 inch square pieces of fiberglass matting and fill the cap with it up past the level of the small holes.
Mix resin and pour it over the cut glass to a point about 1/4 inch above the holes and allow it to dry before removing the cap from the vise. Don’t worry about any resin that leaks out around the base hole. Resin fills the small holes, making the tube strong enough to take the blast when you fire the gun.
When the inside is hardened, turn the assembly over and add glass around the backside of the cap for added strength as shown. Avoid getting resin in the opening where the barrel fits. See figure 13.
Place the finished cap and inner tube on one end of the PVC tubing that has already been cut to size. Center the inner tube as you look in the open end of the PVC.
Now drill a 1/8 inch hole in three place around the tube about 1/4 inch from the lip of the cap.
Take the inner tube out and enlarge the holes in the cap to 3/16 inch. See figure 14.
Replace the inner tube and tighten it down with three small wood screws.
Trim the inside tube down until it extends about 1/2 inch beyond the outside PVC tube.
Sharpen one end of the drill rod to a point and use as a punch. Stand the tube up with the solid cap down. Then drop the drill rod down the inner tube to get a true center mark. See figure 15.
Find a drill bit a little larger than the outside diameter of the inner tube. Remove the cap and drill the hole.
Replace the cap on the open end of the PVC and drill three 1/8 inch holes around the cap as before for wood screw.
Grind off any inner tube that sticks out. make it flush with the face of the cap. See figure 16.
Unfold the sections of steel wool and roll between palms to make strands as shown.
Feed the strands into the silencer tube in a circular motion, packing the wool tight with a stick. Do this until the tube is completely full. See figure 17.
Replace the end cap with the three screws. See figure 18.
Paint the finished silencer black and attach it to your weapons. You may want to ensure proper alignment by wrapping tape or placing a hose clamp around the extension behind the sight. See figure 19.
THE FINISHED PRODUCT
Your finished product is whisper-quiet, the way a silencer is supposed to be! It is inexpensive, effective and reusable for over four hundred rounds before you will need to repack.
This little tool is so easy to make that you will feel no pain when you crush it to bits and throw it away.
I am learning a lot from your site. Sir, can I have the images that are supposed to be attached in this particular article thru email? Thanks!
Thanks a lot for the information. I would also like the pictures that go with these pages by email if possible. It is a little hard to picture how this is sopposed to work without them.
Thanks -M
Very helpfull, thanks sir. Could you email me those pictures, please?